Енергія сталі: репортаж із заводу Interpipe Steel
Запровадження нового ринку електроенергії змусило активізуватися генеруючі, постачальні компанії та включитися в боротьбу за споживача. Особливо цікавими є досить крупні споживачі, потреби яких можуть перевищувати 1 млн кВт-год на добу. До таких зокрема належать підприємства електрометалургії, у виробничому процесі яких електрична енергія посідає центральне місце. Одним із таких споживачів являється сучасне електроплавильне підприємство «Інтерпайп Сталь», яке розташоване в м. Дніпро, входить в групу Interpipe Віктора Пінчука та споживає в місяць біля 50 млн кВт-год електроенергії.
Збудоване «з нуля» у 2012р з проектною потужністю 1,3 млн т сталі в рік італійською компанією Danieli, це підприємство на сьогодні являється не лише лідером на українському чи європейському ринках металопродукції, але й займає провідну позицію у світовому рейтингу виробників трубної продукції та коліс для потреб залізниці. Для ознайомлення гравців ринку електроенергії з таким досить привабливим клієнтом кореспондент ExPro Electricity відвідав підприємство та познайомився з використання електроенергії у технологічному процесі виплавки сталі.
Візит на завод розпочався із інструктажу з техніки безпеки та ознайомлення із унікальною схемою живлення підприємства. За словами директора з корпоративних відносин Interpipe Дмитра Кисилевського, у зв’язку із значним обсягом енергоспоживання «Інтерпайп Сталь» не могла бути підключена до локальних розподільчих мереж, для її забезпечення було використано підключення до недалеко розташованого генеруючого підприємства – Придніпровської ТЕС.

Маршрут прокладання підземного кабелю від ТЕС до заводу
Для підключення заводу був прокладений підземний кабель напругою 330 кВ на відстань 12,8 км, в тому числі під дном річки Самара, яка протікає між електростанцією та територією, де розташоване електроплавильне підприємство.

Структура та переваги підземного кабелю
Варто зауважити, що це унікальний для України проект з використання підземного кабелю такої високої напруги. Для нового кабелю була спеціально розроблена стійка ізоляція.
Підстанція «Пічна» 330 кВ, справа розташовані входи підземного кабелю
Кабель виходить до підстанції «Пічна» 330 кВ, яка була спеціально збудована в 2011р під потреби заводу. На підстанції використане обладнання таких провідних виробників електричного обладнання як шведсько-швейцарської компанії ABB та французької Schneider Electric. Крім самого заводу, Interpipe інвестував $30 млн у будівництво власного підприємства з підготовки металобрухту - основної сировини для виплавки сталі за допомогою електричного розряду.
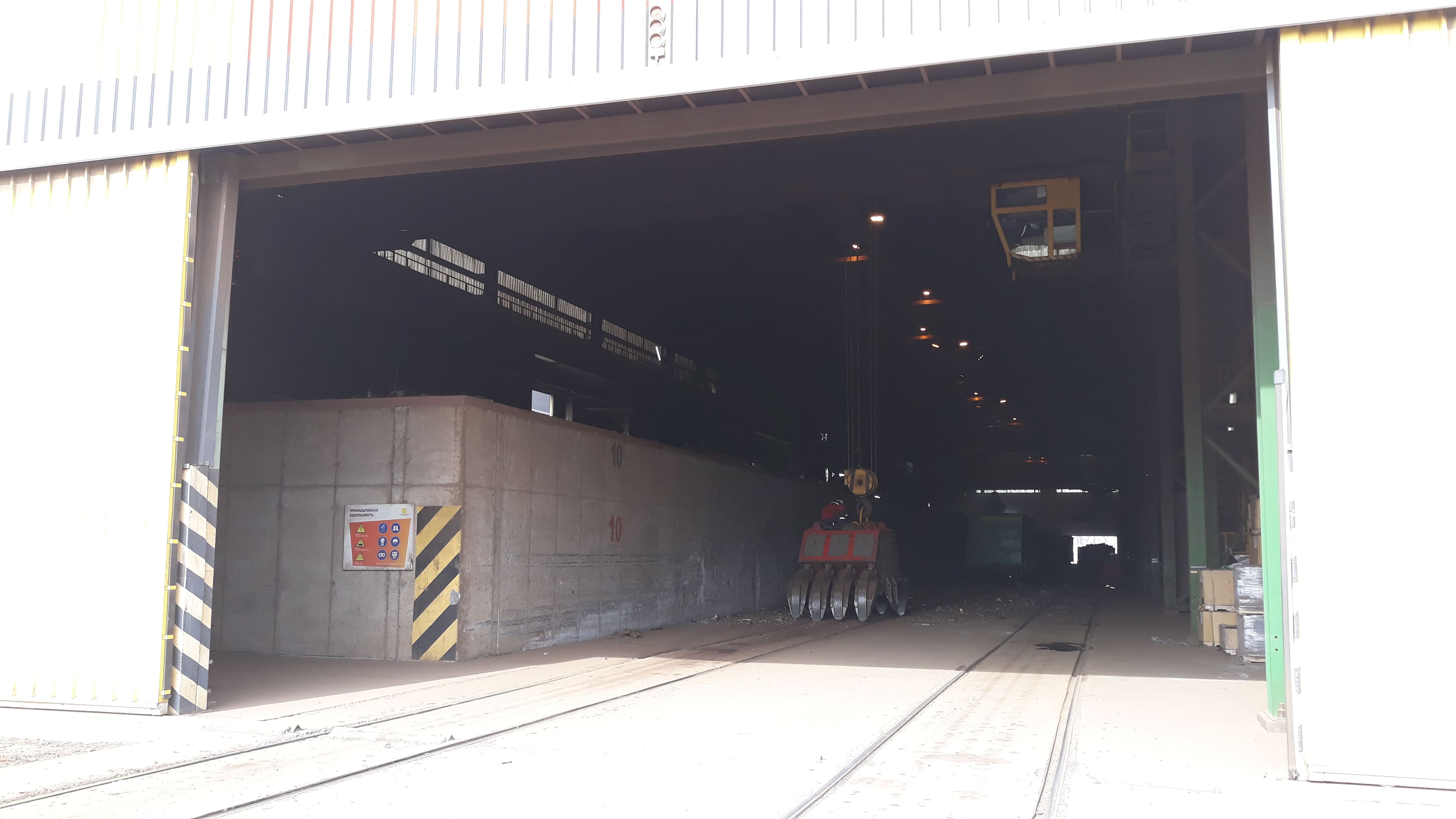
Сюди прибувають напіввагони з металобрухтом
Спеціально відсортований металобрухт залізним транспортом доставляється в цех фасування металобрухту, який називається скрапярд, де зберігаються оперативні запаси (п’ятиденні) цінної сировини. За словами Кисилевського, сучасна електрометалургія на відміну застарілої технології мартенівського виробництва являється «більш ніжною технологією» та вимагає використання спеціально подрібненого металобрухту. Такі вимоги обумовлені тим, щоб не пошкодити електроди, які занурюють в шихту – суміш металобрухту, з якої буде виплавлена сталь для виготовлення труб, або коліс (в такому випадку у шихту додається 15-20 т чавуну).
Після відвідання складу та ознайомлення із газоочисними спорудами, які забезпечують дотримання суворих екологічних стандартів сучасного електрометалургійного виробництва, групу журналістів провели безпосередньо в цехи заводу. Першим, що одразу кинулося в очі було яскраве світло розплавленої сталі, якою був наповнений ківш, який виїжджав із електродугової печі. Сталь плавиться і транспортується у спеціальних ківшах, які одночасно використовуються на багатьох етапах виробництва.

Ківш із 160 тоннами розплавленої сталі вивозять з електродугової печі
Під час процесу плавки на електроди подається напруга 35 кВ. Три графітові електроди опускаються в шихту масою 180-185 тонн та плавлять металобрухт при температурі 1600°С. На виході із печі отримують 160 тонн робочої маси розплавленої сталі (20-25 тонн становить технологічний залишок у ківші). За одну добу на заводі виконується 23-24 операції плавки.

Порції розплавленої сталі чекають своєї черги для мікролегування
В цеху також розташовані ківши, які вже покинули піч та чекають на наступний етап технологічного циклу – доведення розплавленої сталі до необхідного хімічного складу, яка проходить в окремій установці «піч-ківш».

Кран переносить наповнений ківш до установки «піч-ківш»
В цій установці, яка розрахована на два ківши, сталь знову нагрівається за допомогою дугового електричного розряду. Під час цього етапу сталь проходить десульфуризацію (видалення сірки), а також до неї додаються необхідні елементи такі як феросплави, а також алюмінієвий, вуглецевий, титановий, кремнійвмісний та феронікелевий дріт. Використання дроту значно спрощує вимірювання того обсягу елементу, який необхідно додати: знаючи вміст корисного елементу на одиницю довжини дроту, сталеварам, щоб додати точну масу домішки, достатньо відміряти необхідний шматок дроту. Додавання цих легувальних елементів потрібне для досягнення цільових фізичних показників сталі.

Три електроди встановлюються в спеціальні отвори в кришці ківша
Серед великої кількості обладнання, електроди легко помітити завдяки яскравому світлу, яке оточує їх основу та створюється електричною дугою, яка пронизує розплавлену сталь та дозволяє розчинитися в ній корисним домішкам. Після легування, крани переміщують ківш для вакуумної дегазації – процесу вилучення з розплаву газів (кисню, водню, оксидів вуглецю та ін.) завдяки значному пониженню тиску та створення вакууму. Ця стадія вкрай важлива для досягнення високих показників якості сталі.
Вилучивши непотрібні газоподібні сполуки, ківш направляється в машину безперервного лиття заготовок. Ця установка служить для того, щоб розлити розплавлену сталь в необхідну форму.

Розплавлений метал витікає із ківша для подальшого розливу заготовок
Розплавлена сталь рівномірно розподіляється на чотири струмки, які після застигання перетворюються в довгі циліндри – заготовки, які являються напівфабрикатом для подальшого виробництва.

Чотирьохструмкова машина безперервного лиття заготовок

Довгі циліндри розрізаються газовими різками та зберігаються в спеціальних пеналах

Пенали для зберігання гарячих заготовок
В пеналах стальна заготовки витримуються 3-4 доби для остаточного застигання та віддачі тепла. Отриманий металопрокат використовується для виробництва двох видів продукції – труб, які використовуються для видобутку нафти і газу (обсадні та насосно-компресорні) та коліс для залізничного транспорту.

Прес створює тиск на заготовку з масою 10 тис тонн
Після відвідання заводу, групу журналістів провели на територію поряд розташованого «Нижньодніпровського трубопрокатного заводу», який також входить в портфель активів Interpipe. Біля одного із цехів підприємства буквально дрижала земля. Як пояснив заступник начальника колісно-прокатного цеху по наскрізній технології Андрій Кішинський, це працюють масивні преси, які служать для того, щоб сплюснути циліндричну заготовку та надати їй форму колеса. Преси тиснуть на розпечений метал з вагою 5, 10 тисяч тонн. Під час стиснення на колесо подаються струмені води, які необхідні для того, щоб позбутися окалини, яка утворюється на поверхні заготовки.

Виробнича лінія для надання форми залізничну колесу
Колеса проходять декілька етапів стиснення в результаті яких вони отримують необхідну форму, після чого вони направляються в цех, де їх обточують спеціальні автоматизовані машини. За допомогою лазерної техніки та інших вимірювальних приладів, інженери перевіряють якість виготовленого колеса та його відповідність заданим параметрам.

Готова товарна продукція
Крім коліс, компанія Interpipe виготовляє осі та готові колісні пари. Осі виточуються та фарбуються в окремому цеху. В цьому ж цеху за допомогою спеціального пресу на осі надягаються та закріплюються колеса. Надійність кріплення колеса на осі перевіряється на цьому ж пресі, при чому для перевірки застосовується більший тиск ніж для надягання колеса.

Пофарбовані готові осі та колісні пари
За словами Андрія Кішинського, до колісної продукції, яка пред’являються дуже високі вимоги відповідності показникам якості та розміру (з точністю до декількох мікрон), що в першу чергу обумовлено забезпеченням безпеки залізничних перевезень. З захопленням розповідаючи, як підприємство власними силами освоїло високоточну технологію виробництва колісних пар, Кішинський сказав, що на сьогодні Interpipe постачає свою продукцію майже по всьому світу – в країни Європи, Азії, Південної та Північної Америки (в 2018р – 67 країн), а також на внутрішній ринок.
Після проведення екскурсії, у журналістів була можливість поспілкуватися з фінансовим директором Interpipe Денисом Морозовим. Коментуючи реформу ринку електроенергії, він зазначив, що компанія підтримує лібералізацію енергетичного ринку. «Це нормально обирати постачальників, це добре», - сказав він, проте додав, що для потужного металургійного виробництва виникають труднощі з точним прогнозуванням погодинного споживання електроенергії на дві доби наперед, як того вимагають нові реалії. В компанії зазначили, що зупинка або пуск будь-якої установки такого великого виробництва як металургійний завод одразу значно впливає на заявлений графік споживання.
Дмитро Сидоров
ExPro Consulting https://expro.com.ua/statti/energya-stal-reportaj-z-zavodu-interpipe
Запровадження нового ринку електроенергії змусило активізуватися генеруючі, постачальні компанії та включитися в боротьбу за споживача. Особливо цікавими є досить крупні споживачі, потреби яких можуть перевищувати 1 млн кВт-год на добу. До таких зокрема належать підприємства електрометалургії, у виробничому процесі яких електрична енергія посідає центральне місце. Одним із таких споживачів являється сучасне електроплавильне підприємство «Інтерпайп Сталь», яке розташоване в м. Дніпро, входить в групу Interpipe Віктора Пінчука та споживає в місяць біля 50 млн кВт-год електроенергії.
Збудоване «з нуля» у 2012р з проектною потужністю 1,3 млн т сталі в рік італійською компанією Danieli, це підприємство на сьогодні являється не лише лідером на українському чи європейському ринках металопродукції, але й займає провідну позицію у світовому рейтингу виробників трубної продукції та коліс для потреб залізниці. Для ознайомлення гравців ринку електроенергії з таким досить привабливим клієнтом кореспондент ExPro Electricity відвідав підприємство та познайомився з використання електроенергії у технологічному процесі виплавки сталі.
Візит на завод розпочався із інструктажу з техніки безпеки та ознайомлення із унікальною схемою живлення підприємства. За словами директора з корпоративних відносин Interpipe Дмитра Кисилевського, у зв’язку із значним обсягом енергоспоживання «Інтерпайп Сталь» не могла бути підключена до локальних розподільчих мереж, для її забезпечення було використано підключення до недалеко розташованого генеруючого підприємства – Придніпровської ТЕС.

Маршрут прокладання підземного кабелю від ТЕС до заводу
Для підключення заводу був прокладений підземний кабель напругою 330 кВ на відстань 12,8 км, в тому числі під дном річки Самара, яка протікає між електростанцією та територією, де розташоване електроплавильне підприємство.

Структура та переваги підземного кабелю
Варто зауважити, що це унікальний для України проект з використання підземного кабелю такої високої напруги. Для нового кабелю була спеціально розроблена стійка ізоляція.

Підстанція «Пічна» 330 кВ, справа розташовані входи підземного кабелю
Кабель виходить до підстанції «Пічна» 330 кВ, яка була спеціально збудована в 2011р під потреби заводу. На підстанції використане обладнання таких провідних виробників електричного обладнання як шведсько-швейцарської компанії ABB та французької Schneider Electric. Крім самого заводу, Interpipe інвестував $30 млн у будівництво власного підприємства з підготовки металобрухту - основної сировини для виплавки сталі за допомогою електричного розряду.
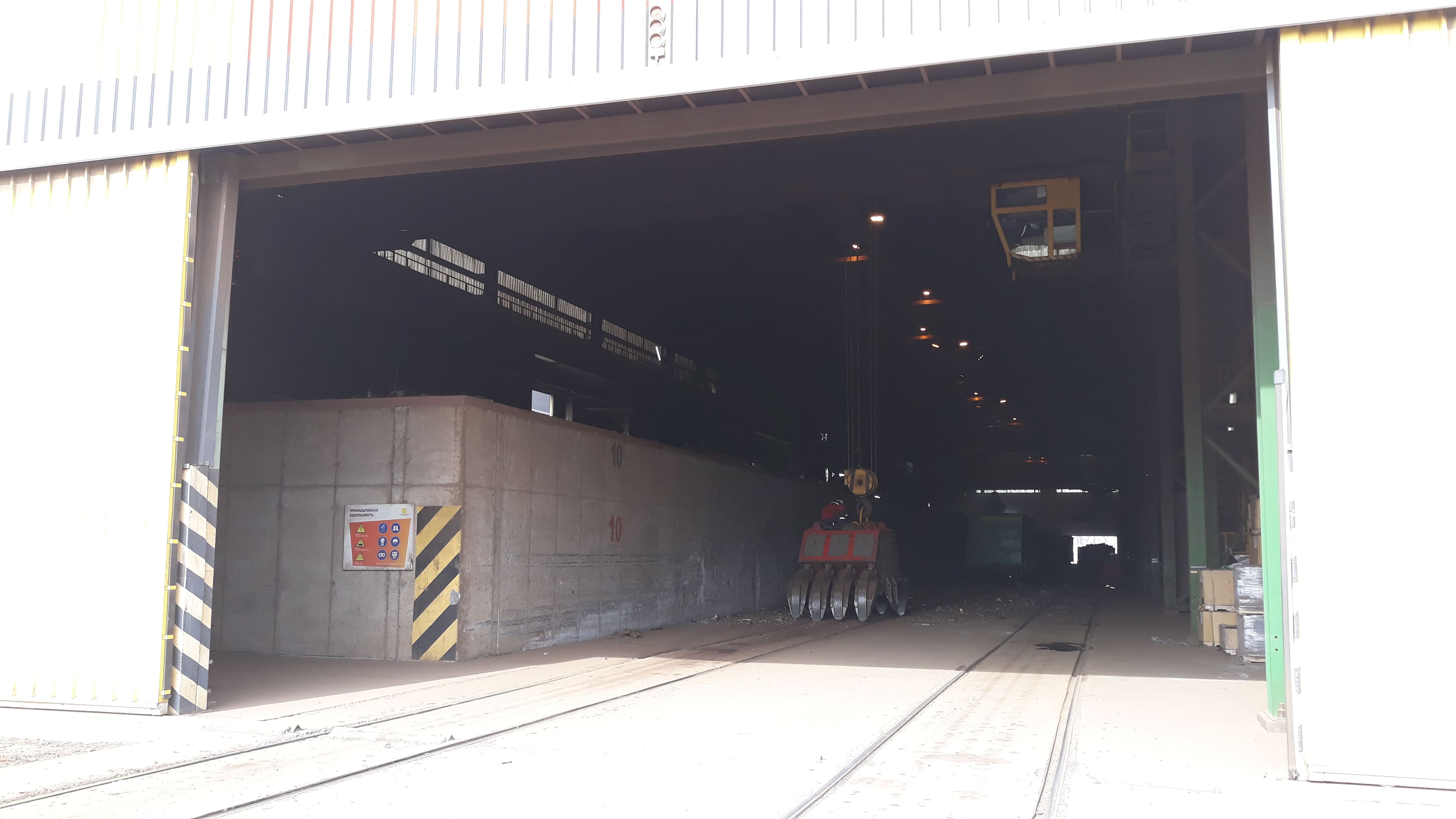
Сюди прибувають напіввагони з металобрухтом
Спеціально відсортований металобрухт залізним транспортом доставляється в цех фасування металобрухту, який називається скрапярд, де зберігаються оперативні запаси (п’ятиденні) цінної сировини. За словами Кисилевського, сучасна електрометалургія на відміну застарілої технології мартенівського виробництва являється «більш ніжною технологією» та вимагає використання спеціально подрібненого металобрухту. Такі вимоги обумовлені тим, щоб не пошкодити електроди, які занурюють в шихту – суміш металобрухту, з якої буде виплавлена сталь для виготовлення труб, або коліс (в такому випадку у шихту додається 15-20 т чавуну).
Після відвідання складу та ознайомлення із газоочисними спорудами, які забезпечують дотримання суворих екологічних стандартів сучасного електрометалургійного виробництва, групу журналістів провели безпосередньо в цехи заводу. Першим, що одразу кинулося в очі було яскраве світло розплавленої сталі, якою був наповнений ківш, який виїжджав із електродугової печі. Сталь плавиться і транспортується у спеціальних ківшах, які одночасно використовуються на багатьох етапах виробництва.

Ківш із 160 тоннами розплавленої сталі вивозять з електродугової печі
Під час процесу плавки на електроди подається напруга 35 кВ. Три графітові електроди опускаються в шихту масою 180-185 тонн та плавлять металобрухт при температурі 1600°С. На виході із печі отримують 160 тонн робочої маси розплавленої сталі (20-25 тонн становить технологічний залишок у ківші). За одну добу на заводі виконується 23-24 операції плавки.

Порції розплавленої сталі чекають своєї черги для мікролегування
В цеху також розташовані ківши, які вже покинули піч та чекають на наступний етап технологічного циклу – доведення розплавленої сталі до необхідного хімічного складу, яка проходить в окремій установці «піч-ківш».

Кран переносить наповнений ківш до установки «піч-ківш»
В цій установці, яка розрахована на два ківши, сталь знову нагрівається за допомогою дугового електричного розряду. Під час цього етапу сталь проходить десульфуризацію (видалення сірки), а також до неї додаються необхідні елементи такі як феросплави, а також алюмінієвий, вуглецевий, титановий, кремнійвмісний та феронікелевий дріт. Використання дроту значно спрощує вимірювання того обсягу елементу, який необхідно додати: знаючи вміст корисного елементу на одиницю довжини дроту, сталеварам, щоб додати точну масу домішки, достатньо відміряти необхідний шматок дроту. Додавання цих легувальних елементів потрібне для досягнення цільових фізичних показників сталі.

Три електроди встановлюються в спеціальні отвори в кришці ківша
Серед великої кількості обладнання, електроди легко помітити завдяки яскравому світлу, яке оточує їх основу та створюється електричною дугою, яка пронизує розплавлену сталь та дозволяє розчинитися в ній корисним домішкам. Після легування, крани переміщують ківш для вакуумної дегазації – процесу вилучення з розплаву газів (кисню, водню, оксидів вуглецю та ін.) завдяки значному пониженню тиску та створення вакууму. Ця стадія вкрай важлива для досягнення високих показників якості сталі.
Вилучивши непотрібні газоподібні сполуки, ківш направляється в машину безперервного лиття заготовок. Ця установка служить для того, щоб розлити розплавлену сталь в необхідну форму.

Розплавлений метал витікає із ківша для подальшого розливу заготовок
Розплавлена сталь рівномірно розподіляється на чотири струмки, які після застигання перетворюються в довгі циліндри – заготовки, які являються напівфабрикатом для подальшого виробництва.

Чотирьохструмкова машина безперервного лиття заготовок

Довгі циліндри розрізаються газовими різками та зберігаються в спеціальних пеналах

Пенали для зберігання гарячих заготовок
В пеналах стальна заготовки витримуються 3-4 доби для остаточного застигання та віддачі тепла. Отриманий металопрокат використовується для виробництва двох видів продукції – труб, які використовуються для видобутку нафти і газу (обсадні та насосно-компресорні) та коліс для залізничного транспорту.

Прес створює тиск на заготовку з масою 10 тис тонн
Після відвідання заводу, групу журналістів провели на територію поряд розташованого «Нижньодніпровського трубопрокатного заводу», який також входить в портфель активів Interpipe. Біля одного із цехів підприємства буквально дрижала земля. Як пояснив заступник начальника колісно-прокатного цеху по наскрізній технології Андрій Кішинський, це працюють масивні преси, які служать для того, щоб сплюснути циліндричну заготовку та надати їй форму колеса. Преси тиснуть на розпечений метал з вагою 5, 10 тисяч тонн. Під час стиснення на колесо подаються струмені води, які необхідні для того, щоб позбутися окалини, яка утворюється на поверхні заготовки.

Виробнича лінія для надання форми залізничну колесу
Колеса проходять декілька етапів стиснення в результаті яких вони отримують необхідну форму, після чого вони направляються в цех, де їх обточують спеціальні автоматизовані машини. За допомогою лазерної техніки та інших вимірювальних приладів, інженери перевіряють якість виготовленого колеса та його відповідність заданим параметрам.

Готова товарна продукція
Крім коліс, компанія Interpipe виготовляє осі та готові колісні пари. Осі виточуються та фарбуються в окремому цеху. В цьому ж цеху за допомогою спеціального пресу на осі надягаються та закріплюються колеса. Надійність кріплення колеса на осі перевіряється на цьому ж пресі, при чому для перевірки застосовується більший тиск ніж для надягання колеса.

Пофарбовані готові осі та колісні пари
За словами Андрія Кішинського, до колісної продукції, яка пред’являються дуже високі вимоги відповідності показникам якості та розміру (з точністю до декількох мікрон), що в першу чергу обумовлено забезпеченням безпеки залізничних перевезень. З захопленням розповідаючи, як підприємство власними силами освоїло високоточну технологію виробництва колісних пар, Кішинський сказав, що на сьогодні Interpipe постачає свою продукцію майже по всьому світу – в країни Європи, Азії, Південної та Північної Америки (в 2018р – 67 країн), а також на внутрішній ринок.
Після проведення екскурсії, у журналістів була можливість поспілкуватися з фінансовим директором Interpipe Денисом Морозовим. Коментуючи реформу ринку електроенергії, він зазначив, що компанія підтримує лібералізацію енергетичного ринку. «Це нормально обирати постачальників, це добре», - сказав він, проте додав, що для потужного металургійного виробництва виникають труднощі з точним прогнозуванням погодинного споживання електроенергії на дві доби наперед, як того вимагають нові реалії. В компанії зазначили, що зупинка або пуск будь-якої установки такого великого виробництва як металургійний завод одразу значно впливає на заявлений графік споживання.
Дмитро Сидоров
ExPro Consulting https://expro.com.ua/statti/energya-stal-reportaj-z-zavodu-interpipe